Differential Pressure
The change in pressure from the feed water inlet to the concentrate outlet is known as differential pressure (dP), where differential pressure is one of the key performance indicators of the energy efficiency of an RO system. A higher dP increases energy consumption and, at a certain point, may even cause irreversible membrane damage. In addition, it can also affect the fouling behavior and cleaning efficiency in the membrane system operation.
In response, LG Chem has developed a new feed spacer to minimize flow disturbance and pressure losses in an RO element. Moreover, the new spacer enhances fouling resistance, thus reducing the need for chemical cleaning and overall plant downtime.
Key Features of Novel Spacer
The primary function of a feed spacer is to separate two membrane leaves allowing the feed stream to freely flow
between membrane leaves while creating turbulence to minimize concentration polarization. Broadly described,
the latter phenomenon is the accumulation of solutes near the membrane surface, leading to membrane
performance degradation. As the feedwater passes through the RO element, it loses pressure due to overcoming feed spacer resistance, which is how differential pressure forms. At constant operating conditions, the differential pressure depends on the geometry of the membrane feed spacer that includes mesh size, strand diameter and its shape, and the angle between the adjacent strands. To improve the spacer design, LG Chem researchers experimented with spacer configurations to achieve optimal flow and low resistance while maintaining a sufficient level of turbulence and mechanical integrity of the mesh spacer.
The result is the new L spacer, a 34-mil thickness mesh with improved strand arrangement and geometry that minimizes flow disturbance and pressure losses without increasing concentration polarization.
The following are field results demonstrating the effectiveness of LG Chem’s novel L feed spacer at
reducing differential pressure (dP) in RO systems.
Indirect Potable Reuse System
A pilot study at a wastewater reuse system for indirect potable reuse in California compared several leading low fouling
RO membranes for differential pressure. Figure 1 shows that the LG NanoH₂O™ RO membrane with the novel L spacer significantly lowers differential pressure than other membrane models tested.
System configuration: 7 elements per pressure vessel, Flux: 25.3 lmh (14.9 gfd), Recovery rate: 55%.
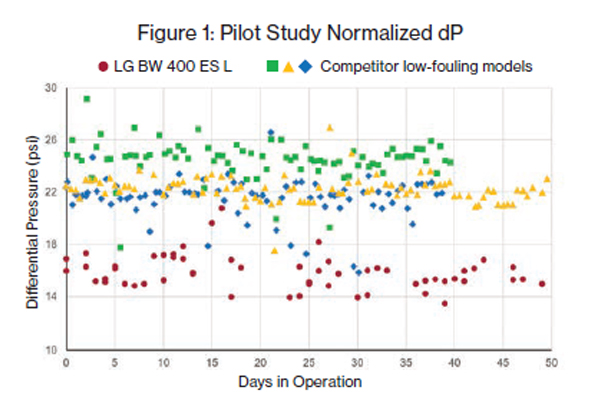
Alamogordo, New Mexico
A pilot study at the Brackish Groundwater National Desalination Research Facility (BGNDRF), run by the US Bureau of Reclamation, showed a significantly lower differential pressure by LG NanoH₂O™ membrane with the novel L spacer when compared to a competitor’s leading product (11,500 gpd, 99.7% rejection, 34-mil low dP spacer); see Figure 2.
System configuration: 7 elements per pressure vessel, Flux: 25.0 lmh (14.7 gfd), Recovery rate: 50%.
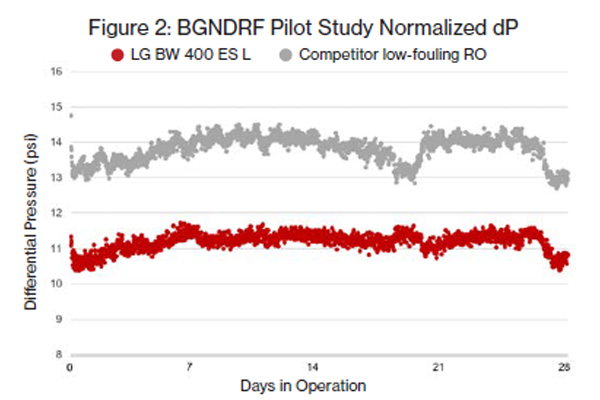
Industrial Wastewater Reuse
A major steel manufacturing facility, treating its wastewater for reuse back into the industrial process, tested LG NanoH₂O™ membranes against a competitor’s low-fouling membrane element for eight (8) months. As shown in Figure 3, the differential pressure of LG Chem’s RO membrane remained lower than that of the competitor’s product. Moreover, during the pilot study, the plant performed five (5) CIP’s on the competitor’s membrane, while only two (2) CIP’s were required for NanoH₂O™. This example demonstrates the advantage of LG Chem’s new L spacer for reducing chemical cleaning frequency and enhancing plant uptime.
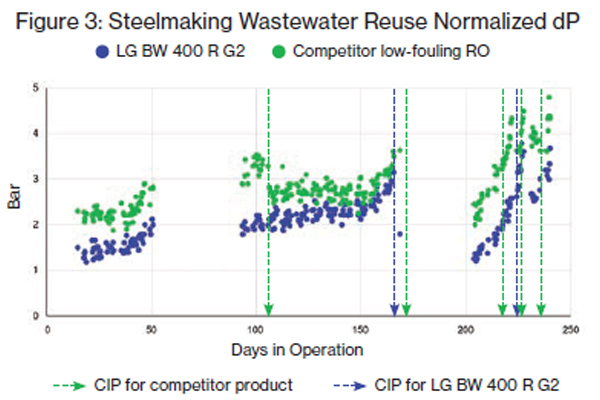
The “L spacer” lower differential pressure at the same high process efficiency and
- Delays the onset of fouling during system operation
- Reduces fouling rate
- Improves chemical cleaning efficiency
Contact LG Water Solutions today to find out how we can optimize your RO system performance and Maximize Plant Uptime.