Case Study
Background
Due to recent droughts in Taiwan, the government began enforcing water conservation policies to regulate water intensive
industrial end-users to reuse 70–85% of their wastewater. To comply and remain commercially viable, global optoelectronic company in Taiwan (TFT-LCD panel production) implemented a zero liquid discharge (ZLD) process to maximize water recovery. Using an advanced MBR-RO-EDR* membrane treatment system, the company has successfully recycled an average of 91% of its process water in recent years.
System Information
The wastewater influent is a mixture of waste streams collected from various stages of the panel production line. The water quality, as a result, is a complex makeup of contaminants (Table 1) and creates a challenging scenario for treatment. However, once the MBR reduces suspended solid levels, the RO and EDR ensure ultrapure water quality for reuse.
Table 1: Feed Water Makeup | |
Item | Feed water range |
BOD | 200–400 mg/L |
COD | 600–1,000 mg/L |
Total Nitrogen (TN) | 30–50 mg/L |
Total Suspended Solids (TSS) | 50–200 mg/L |
Total Dissolved Solids (TDS) | 750–1,500 mg/L |
pH | 2–12 |
LG BW 400 R G2, LG Chem’s highest rejection brackish water membrane with the new L feed spacer for reducing
differential pressure, was selected as part of the optoelectronic company’s technology procurement strategy
to deliver long-term stable production of high-quality permeate with minimal fouling, cleaning requirements, and
energy consumption. The operating conditions are listed in Table 2.
Table 2: System Information | |
RO feed water | MBR treated effluent |
RO system | 3 trains with 12:8 system array (4M) |
System recovery | 75–78% |
System capacity | 2,880 m3/d |
Feed temperature | 25–30 C |
Feed pressure | 7–9 bar |
Membrane Performance
Compared to the alternative RO (non-TFN membrane) product operated at the plant, NanoH₂O™ membranes showed better and more reliable normalized permeate flow (Figure 1) and salt passage (Figure 2). Furthermore, NanoH₂O™ membranes required more than half fewer cleaning frequencies versus the non-TFN membrane, leading to notable savings in labor, chemical use, and plant downtime (Figure 1). Despite the complex ionic species composition of the wastewater, NanoH₂O™ membranes achieved high-quality permeate requirements for reuse (Table 3). LG BW 400 R G2 is a robust RO membrane element that helped lower the O&M costs of the wastewater recycling facility and realize the water conservation goals of the optoelectronic company.
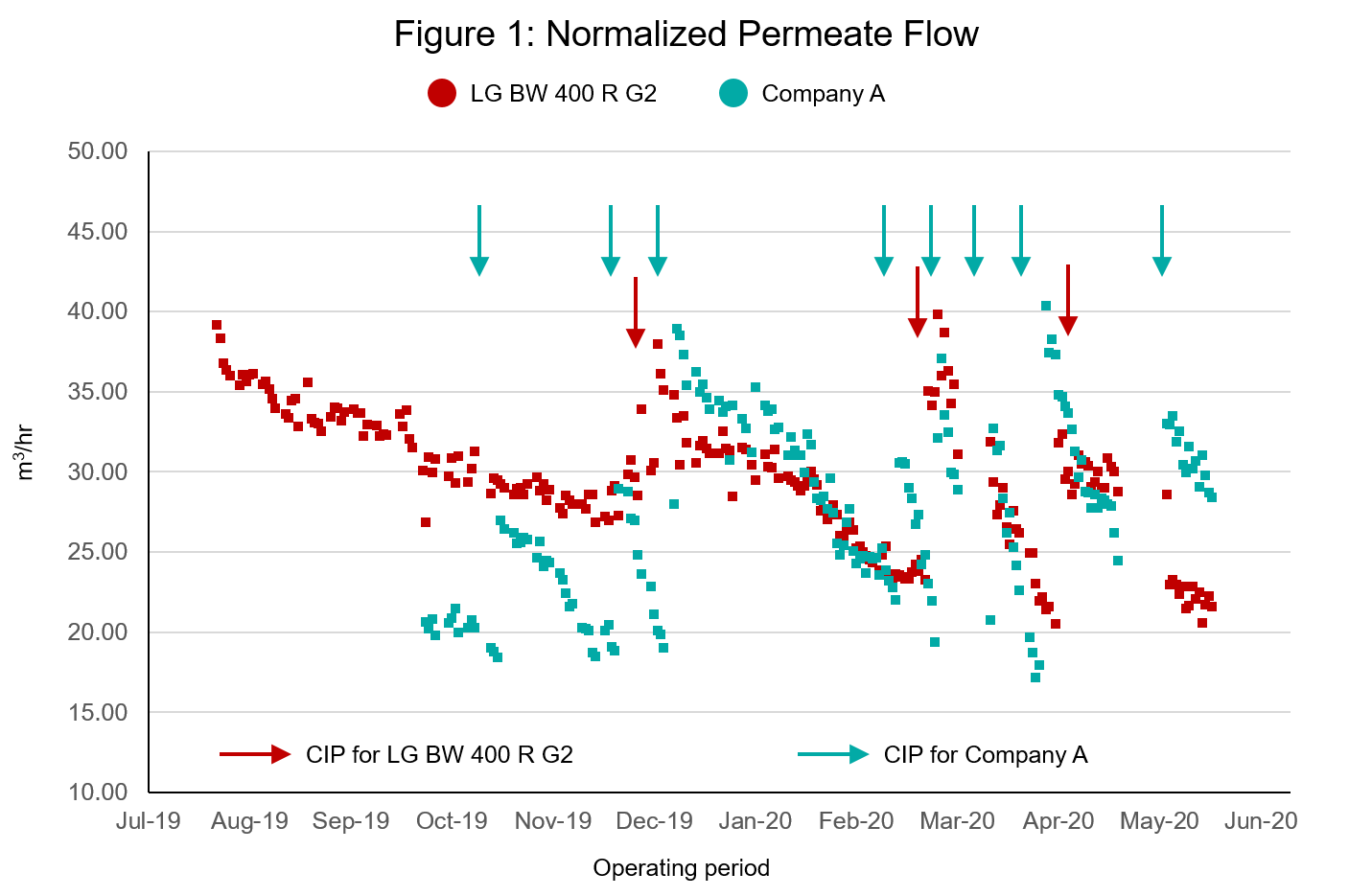
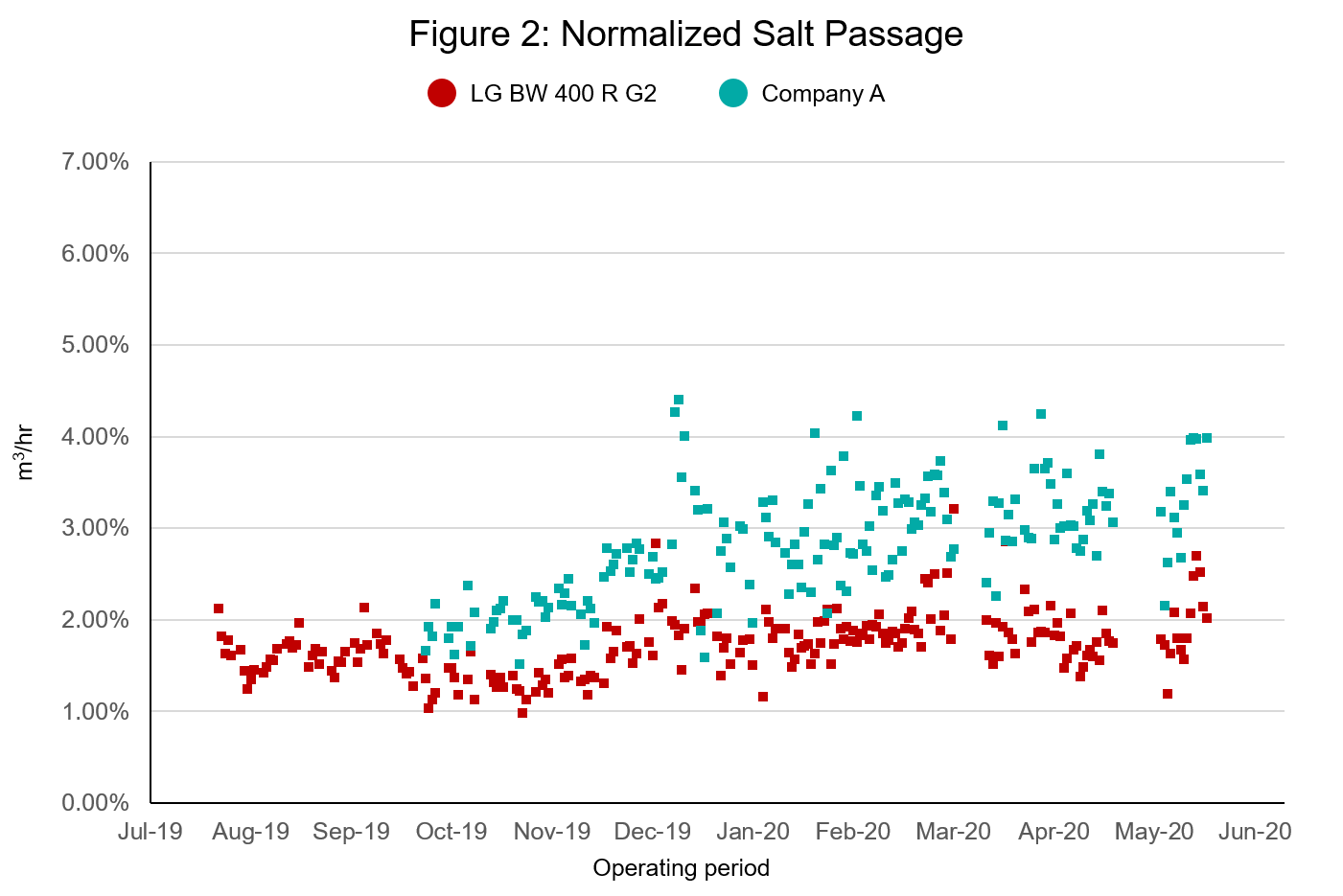
Table 3: Water Quality Analysis | ||||
Item | Unit | Feed | Permeate | Rejection (%) |
Al | mg/L | 0.482 | <0.025 | >94.0 |
Mg | mg/L | 1.75 | 0.082 | 95.3 |
Ca | mg/L | 4.44 | 0.486 | 89.1 |
Na | mg/L | 223 | 3.65 | 98.4 |
Cl | mg/L | 47.6 | 0.27 | 99.4 |
F | mg/L | 23.6 | 1.01 | 95.7 |
NO3 | mg/L | 41.1 | 1.36 | 96.7 |
SO4 | mg/L | 88.5 | ND | >99.9 |
PO4 | mg/L | 415 | ND | >99.9 |
CO3 | mg CaCO3/L | <1.0 | <1.0 | |
HCO3 | mg CaCO3/L | 93.0 | 4.0 | 95.7 |
SiO2 | mg/L | 4.63 | 0.288 | 93.8 |
TOC | mg C/L | 5.1 | <0.5 | >90.2 |